Powder Coating
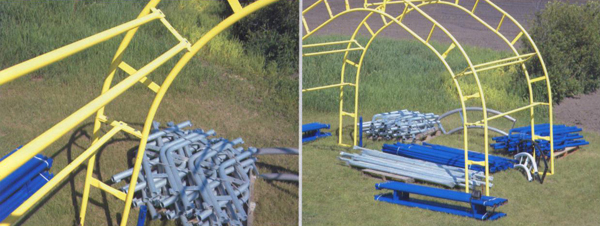
Powder coating is by far the youngest of the surface finishing techniques in common use today. It was first used in Australia about 1967.
Powder coating is the technique of applying dry paint to a part. The final cured coating is the same as a 2-pack wet paint. In normal wet painting such as house paints, the solids are in suspension in a liquid carrier, which must evaporate before the solid paint coating is produced.
In powder coating, the powdered paint may be applied by either of two techniques.
- The item is lowered into a fluidised bed of the powder, which may or may not be electrostatically charged, or
- The powdered paint is electrostatically charged and sprayed onto the part.
The part is then placed in an oven and the powder particles melt and coalesce to form a continuous film.
There are two main types of powder available to the surface finisher:
- Thermoplastic powders that will remelt when heated, and
- Thermosetting powders that will not remelt upon reheating. During the curing process (in the oven) a chemical cross-linking reaction is triggered at the curing temperature and it is this chemical reaction which gives the powder coating many of its desirable properties.
Powder coating is an advanced process of applying powder consisting of finally ground resin and pigment to any surface that can withstand temperature of 375F. The coated item is then placed in a curing oven, resulting in a high quality, long lasting finish.
Items that are powder coated simply last longer. Products with a coated finish are far more resistant to scratching, chipping, fading, rusting and wearing than other finishes. Finishes can range from smooth to wrinkled, matted finishes, or rough textures which hide surface imperfections. You can be assured that our powder coating process is environmentally friendly and unlike paint there is no drying or flash time. Powder coat will virtually never run or drip so your part will have a high quality and durable finish.