Hot-Dip Galvanizing - Your Best Corrosion Protection
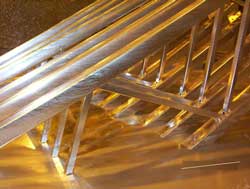
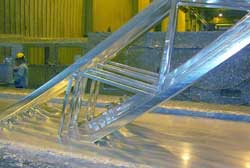
Galvanizing is a process by which a metallurgical reaction binds zinc to steel; however, not all galvanizing techniques are the same.
There are two types of galvanizing meant to protect steel from the damaging effects of corrosion:
- Batch hot dip galvanizing (“HDG”)
- In-line galvanizing (“shielding”)
Hot dip galvanizing is the only process that meets ASTM 123 standards for corrosion protection of steel. The process includes taking a finished fabricated steel member and putting it through a series of chemical baths. The final process is dipping it into an 840° zinc bath, which chemically bonds the zinc to the steel. Once dipped, a minimum 3.9 mils (1 mil= 1/1000th of an inch) bond is formed and the bonded material is now galvanized. The final step in the process is to expose the newly galvanized material to a natural cycle of temperature and atmospheric change. This causes a patina to form on the zinc and provides maximum protection to the steel.
In-line (“shielded”) galvanizing is similar to hot dip galvanizing in that zinc fixes to steel but the process occurs prior to fabrication only 0.9 mils (less than 1/1000th of an inch) of zinc has bonded to the steel. Unfortunately, the fabricator then burns off this thin layer of zinc as the steel is welded. Once the structure is welded, the fabricator uses a zinc-laden spray paint and covers only the outside of the welds. This process is often inadequate and leaves pinholes in the area, which begin to rust immediately. The inside joints are left completely unprotected, allowing water vapor and dust to settle on raw steel.
Horizon Structures uses only hot dip galvanized steel in its structures for maximum corrosion protection.
Additional information about hot dip galvanizing: